BMW engine boss discusses balancing EV, ICE future at Austrian production hub
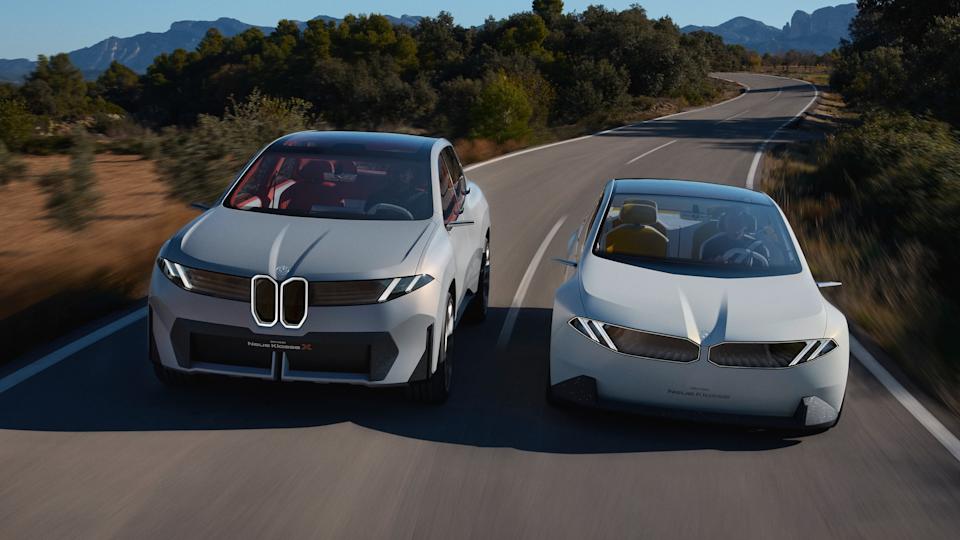
.b-lead-art {display:none;}
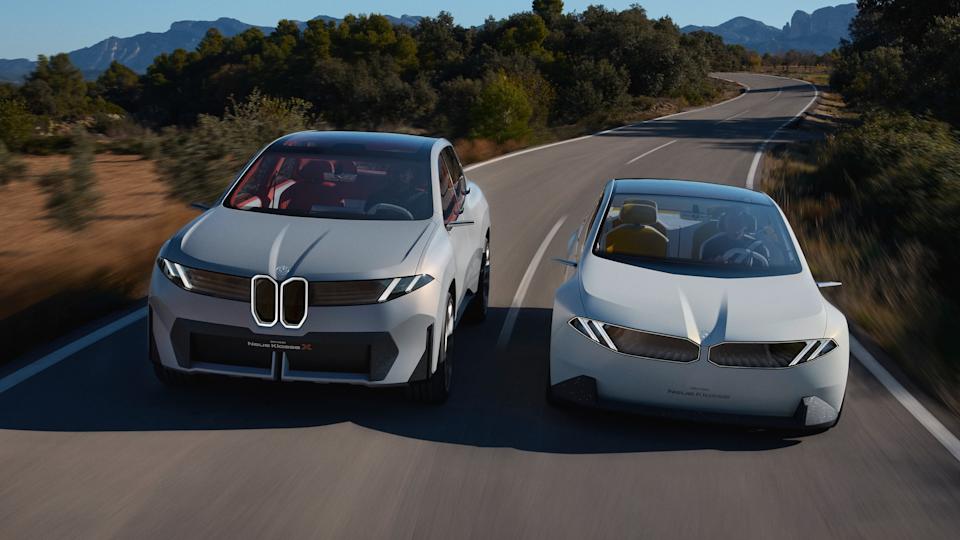
BERLIN — BMW’s plant in Steyr, Austria, is navigating a complex transformation as it expands into electric-powertrain production while maintaining its role as a global hub for combustion-engine manufacturing, the automaker’s head of global powertrain production, Klaus von Moltke, said.
In an interview with Automotive News Europe sibling publication Automobilwoche, von Moltke, who is also head of the Steyr plant, discussed the continued development of diesel and gasoline engines, the production ramp-up for BMW’s Neue Klasse EV architecture, and how employee cross-training and digitalization are helping future-proof operations.
BMW is positioning the Steyr facility as a dual powerhouse for internal combustion and electric drive systems, ensuring a flexible and future-ready supply model for its global vehicle lineup.
With 4,900 employees and €4.4 billion ($5.1 billion) in sales last year, Steyr ranks among Austria’s top 10 industrial sites and is the center of BMW’s global strategy to balance legacy and future propulsion systems.
Sign up for the Automotive News Europe Cars & Concepts newsletter, which covers the biggest moves in Europe’s product market.
“We are very proud at the Steyr site,” von Moltke told Automobilwoche.
The facility was designated in 2022 as the global development and production hub for the upcoming Neue Klasse platform.
The transition was not without uncertainty. “There was definitely a lot of unrest during the preparation phase,” von Moltke said.
With Steyr heavily reliant on combustion engines, the local workforce faced questions about long-term viability.
That changed with the company’s decision to make Steyr a center for EV systems — a move von Moltke said “gives us security for the future beyond 2030.”
The decision hinged on Steyr’s combination of production and development capabilities.
Steyr benefits from development and production at one site
“We have both development and production at one location,” von Moltke said. “This was certainly a strategic advantage because we can industrialize good ideas in the shortest possible time.”
However, BMW is not walking away from its combustion-engine business. “The combustion engine is our foundation and also finances the business of the future,” von Moltke said.
The site produced about 1.2 million combustion engines last year, supplying global markets.
BMW continues to invest in improving traditional engines, including compatibility with new fuels such as HVO100 for diesel and compliance with the upcoming Euro 7 emissions standard.
“We are continuing to develop the technology,” von Moltke said, noting that the long-term vision includes a strong focus on technological flexibility.
“We are open to all technologies and offer all options without creating overcapacity,” he said. “Our task is to position ourselves so that we can serve the markets optimally.”
To support this dual-track approach, BMW is pursuing flexible production and cross-trained workers.
“Our aim is for all employees to be able to work on all technologies,” von Moltke said. “We have highly flexible production systems that can serve both worlds.”
The transition to EV production has also introduced new technical components, such as the inverter — a high-efficiency, high-precision part manufactured under cleanroom conditions.
“Until now, we have purchased this component externally,” von Moltke said. “We see the inverter as a component that sets us apart from the competition and offers considerable potential for further developing the efficiency and performance of electric drives.”
BMW saves energy, weight with latest EV drives
Comparing BMW’s current Gen 5 EV drives with the upcoming Gen 6, von Moltke said the progress is already measurable. “We have reduced energy losses by 40 percent and significantly reduced weight, leading to a 30 percent improvement in vehicle range.”
However, the transition is not finished, with digitalization in the manufacturing process playing a key role, particularly because of Steyr’s high-cost location.
“Digitalization is therefore an important enabler for the future viability of the plant,” von Moltke said.
Despite assumptions that electric-drive production is simpler, von Moltke said the reality is more nuanced.
“We are on a par with the complementing of a combustion engine in terms of work content and depth of work,” he said, noting that BMW’s approach covers deep integration of stator, rotor and transmission components.
This also informs the company’s staffing strategy.
“Our plans are to maintain the current level of staffing until 2030 — around 4,900 employees, 700 of whom work in development,” von Moltke said.
On production capacity, BMW expects to continue producing 1.2 million combustion engines annually, while electric drive capacity will ramp up to 600,000 units across two lines.
“The ratio [of combustion to electric drive production] will develop in line with market demand,” he said.
Steyr’s role in the Neue Klasse is well underway. After BMW’s September 2022 decision, the site moved quickly to complete buildings and install equipment.
“By last summer, we had installed the equipment, after which we delivered the first pre-series components from the site to the Neue Klasse production facility in Debrecen,” von Moltke said.
Output of BMW iX3 will begin in the autumn
Series production for the first Neue Klasse model, the iX3, will begin in BMW’s new factory in Debrecen, Hungary, in the autumn. Pre-series production for a second line will also start around the same time.
Steyr will serve all global markets except China, where BMW operates separate localized engine production.
“This has less to do with tariffs than with market proximity and the necessary supplier network,” von Moltke said.
Addressing whether production might expand globally if demand increases, von Moltke said the company regularly reviews all production scenarios.
“If the ramp-up requires it, we also have a scenario for that,” he said.
As for the EU’s 2035 deadline for ending internal combustion engine sales, von Moltke declined to speculate.
“Our job is to go through all possible scenarios, prepare for each one and ensure that we are able to deliver,” he said.
Another looming challenge is the potential raw material risks for electric motors. While rare earths are not relevant for the new SSM drive system being launched, von Moltke acknowledged concerns about recent Chinese regulations on export licenses.
For now, he said, “our production ramp-up is not at risk,” he said, pointing out that BMW’s approach is about flexibility.
“We have made the investments, the facilities are ready for series production, we are flexibly positioned and the team is able to ensure a consistent supply,” von Moltke said.

The BMW engine boss's strategic discussion on harmonizing the future of electric vehicles (EV) and internal combustion engines(ICE), held at their Austrian production hub, underscores a committed approach to ensuring sustainable innovation while preserving traditional automotives expertise.

BMW's engine strategist offering insights into the intricate dance between electric vehicle (EV) and internal combustion engines(ICE)' future at their Austrian production hub, highlighting how to strike an efficient balance.

The CEO's thoughtful exploration of harmonizing the future for both electric (EV) and internal combustion engine(ICE)-based vehicles at BMW Austria serves as a compelling reminder that excitement lies in finding sustainable coexistence—not dichotomy.